10W TUYA APP kontrolli vedesulkoinen LED seinävalo kotitoimistolle puutarhakoristeelle moderneja koristeita sisä- ja ulkoilmo-valotus
- Yleiskatsaus
- Liittyvät tuotteet
Markkinointitoiminta
Tuotekuvaukset
Tuotteen nimi |
10W TUYA APP -ohjaus vedenkestävä LED-seinävalaisin kotiin, toimistoon, puutarhaan koristeeksi moderni koristeellinen sisä- ja ulkovalaistus ulkovalaistus
|

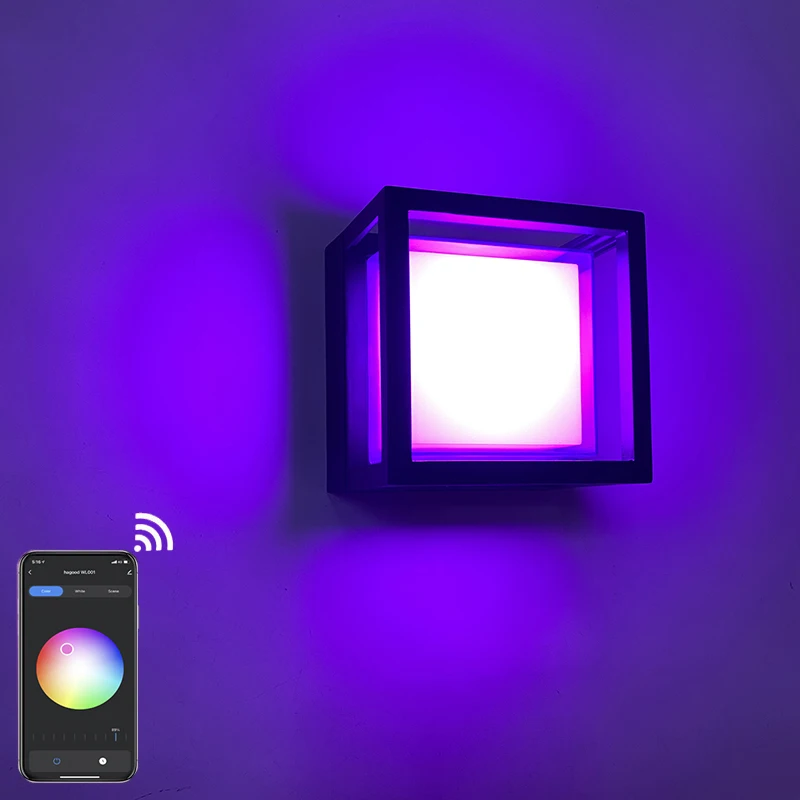
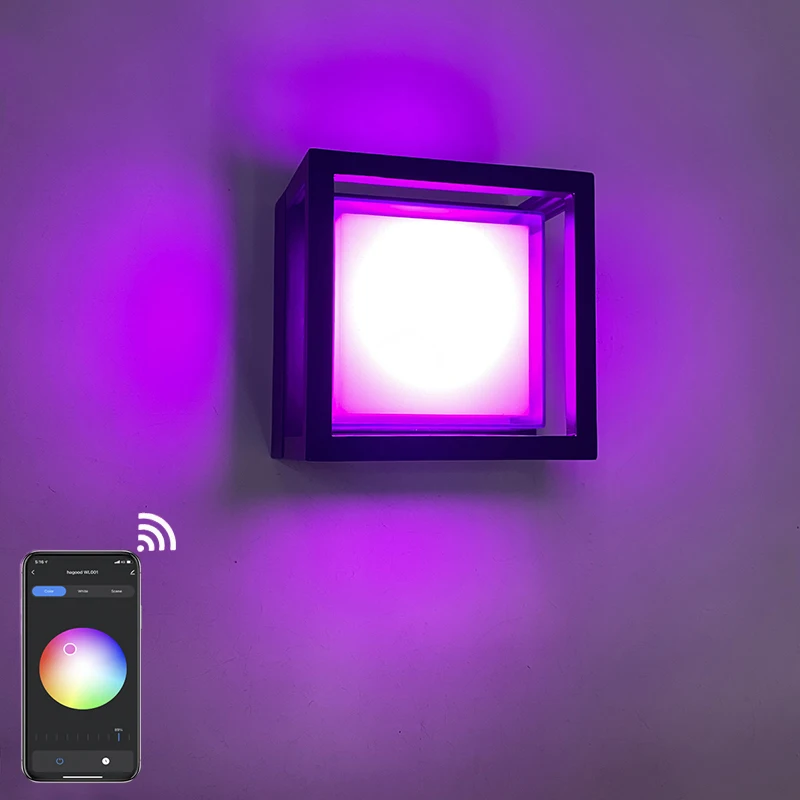
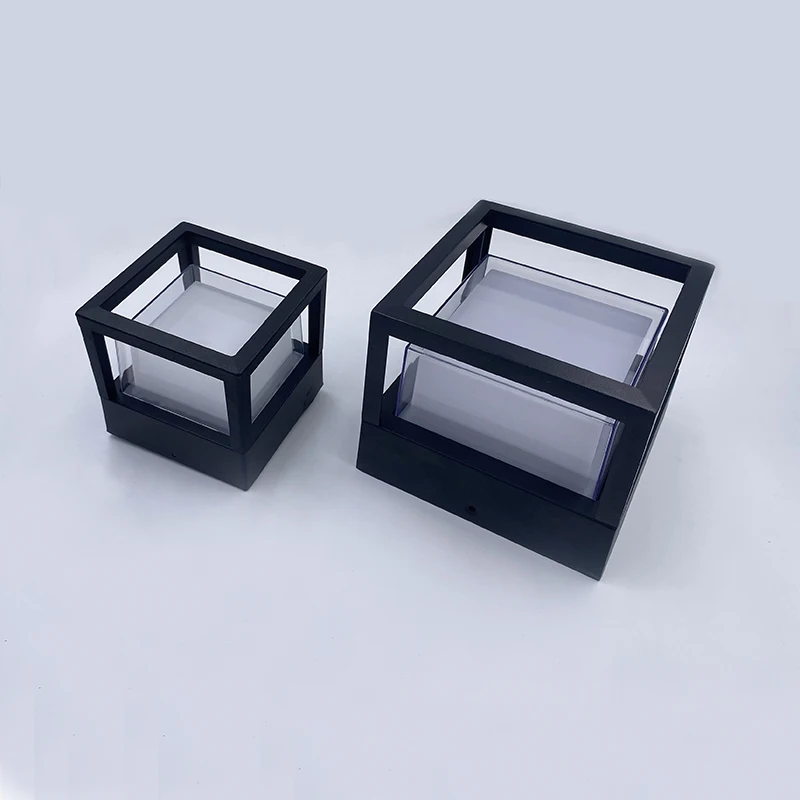
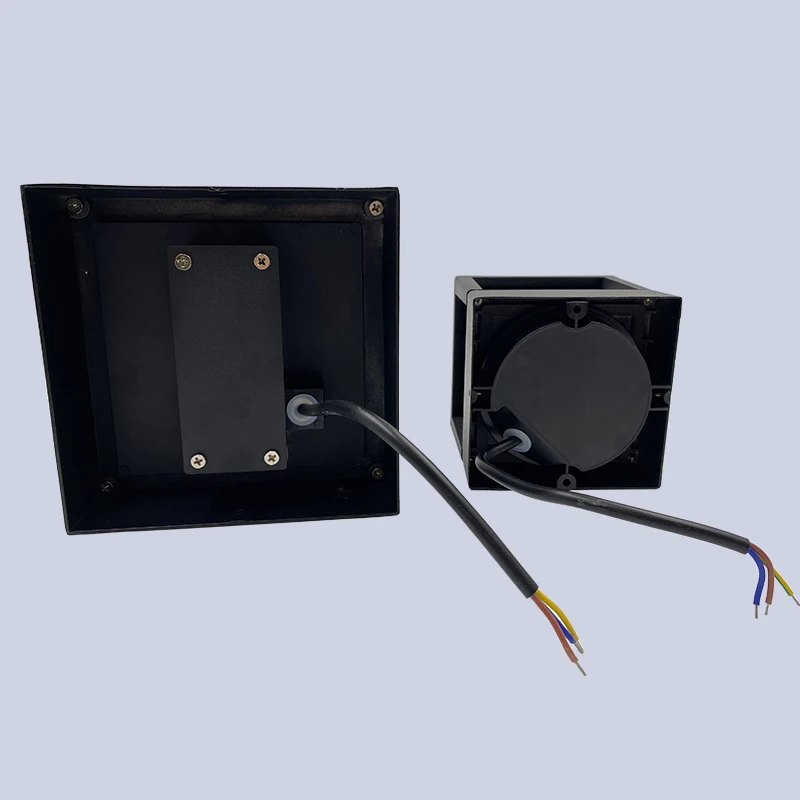

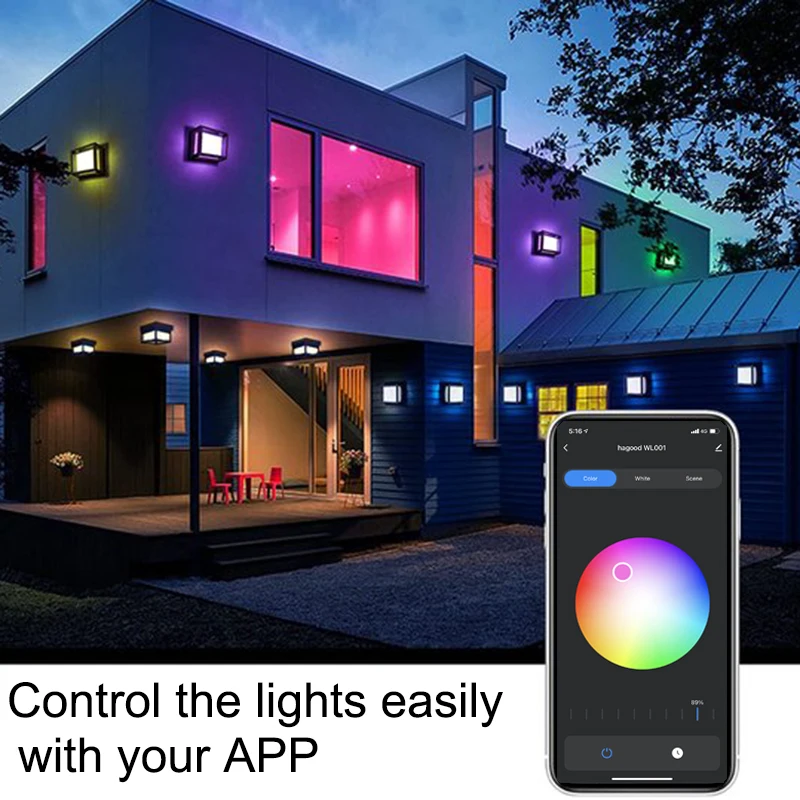
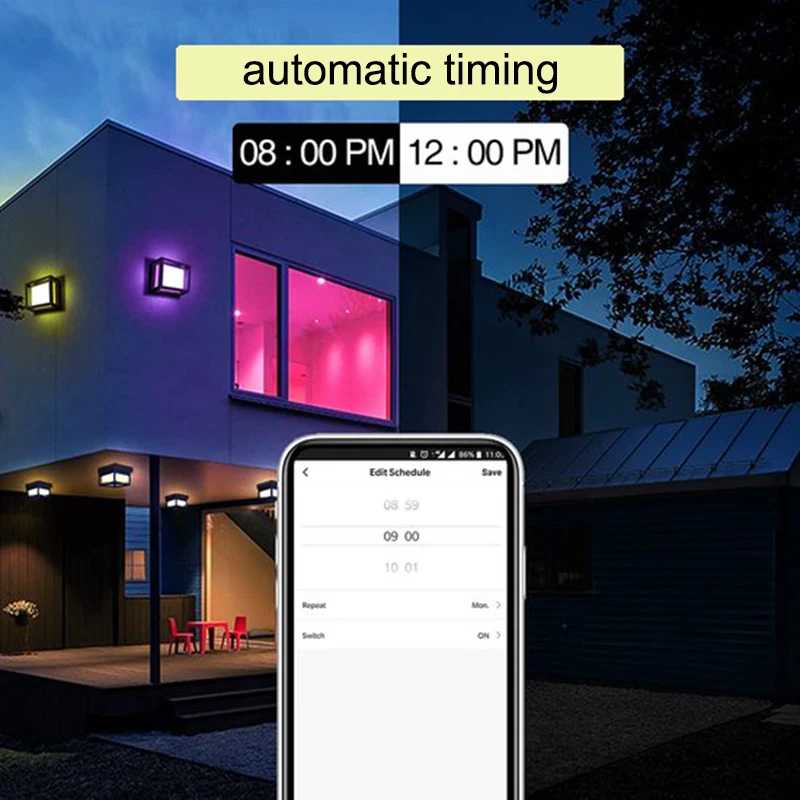
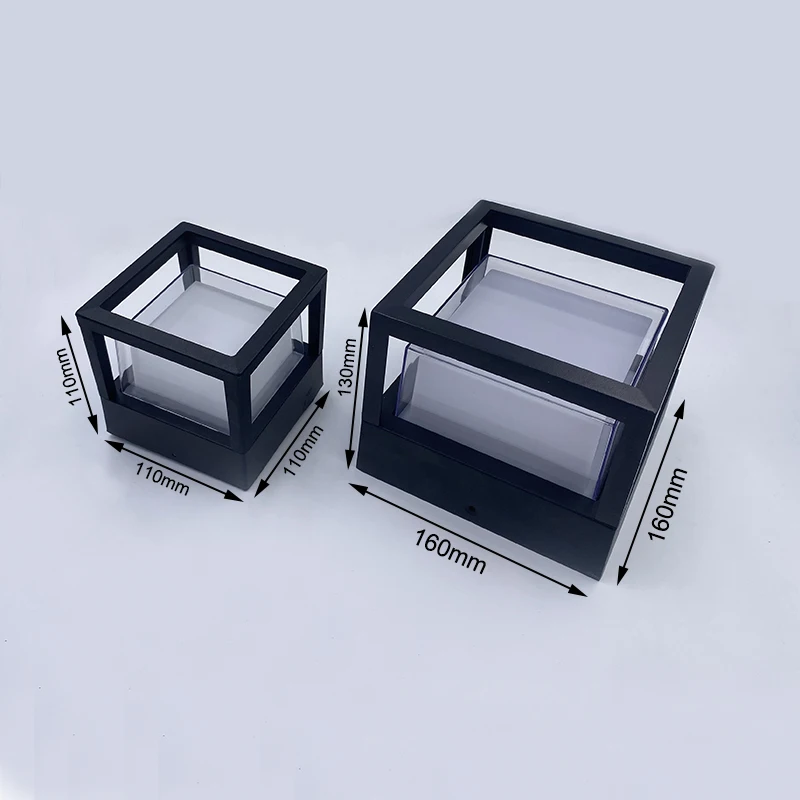
FAQ
Q1: Mitkä ovat uusien asiakkaiden maksuehdot?
V: Yleensä kaupan vakuutus, valinnainen on luottokortti, viisumi, E-tarkastus, Western Union tai T / T.
Q2: Entä läpimenoaika?
V: 3-5 päivää polkujärjestykseen ja 10-15 päivää messuille.
Q3: Kuinka lähetät tavarat ja kuinka kauan niiden saapuminen kestää?
V: Toimitamme yleensä DHL:n, UPS:n, FedExin tai TNT:n kautta. Yleensä saapuminen kestää 3-5 päivää. Toimitus ilmasta ovelle kestää noin 15 päivää.
Q4: Voinko tulostaa logoni telineeseen ja pakkaukseen?
V: Kyllä, EI MOQ:ta logon tulostamiseksi telineeseen ja pakkaukseen.
Q5. Onko tuotteillesi sertifikaatteja?
-- CE, ROHS, PSE, Reach, UKCA jne., jotta ne voidaan myydä maailmanlaajuisesti turvallisesti!
Q6. Kuinka edetä led-valon tilauksessa?
V: Kerro meille ensin vaatimuksistasi tai sovelluksestasi. Toiseksi, laadumme tarjoukset täsmälleen vaatimuksesi tai ehdotustemme mukaan. Kolmanneksi asiakas vahvistaa näytteet ja asettaa talletuksen muodollista tilausta varten. Lopuksi järjestämme tuotannon.
Q7: Kuinka lähetät tavarat ja kuinka kauan niiden saapuminen kestää?
V: Pieni tilaus toimitetaan International Expressillä (3-7 päivää) tai kansainvälisellä logistiikkapaketilla (15-20 päivää). Joukkotilaus toimitetaan lentoyhtiön kautta (5-7 päivää lentokentältä lentokentälle) ja merikuljetus (20-40 päivää DDP)
Q8.Kuinka teet liiketoiminnastamme pitkäaikaisen ja hyvän suhteen?
-1. kilpailukykyinen hinta, jotta win-win
-2. säilytä salaisuudet kaikille yhteistyökykyisille asiakkaillemme
-3. Lähetä uudet vaihtotuotteet seuraavan tilauksen yhteydessä, jos ne ovat viallisia.